Revolutionise your fulfilment with PickEngine
The PickEngine automated storage and retrieval system (AS/RS) is made up of three standardised modules, which you can adjust to meet your needs and open up new opportunities for your order fulfilment. The modular design also keeps implementation times short – under six months, to be precise. PickEngine is innovative and based on storage technology that has proven its worth a thousand times over.
Pick Module
Pick Module
Specially designed ergonomic goods-to-person work stations for decanting and order picking :
- Each work station has access to all items
- Decanting and order fulfilment
- Intelligent user guidance
- Short training times for employees
- Optimum ergonomics
- Maximum performance with minimum personnel costs
Storage Module
Storage Module
Intelligent storage robots keep track of everything in the rack and automatically store and retrieve containers.
- Intelligent Store Bots, top speed 4 m/s
- Rack width: approx. 5.5 m
- Rack height: 10 m
- Rack length: scalable from 35 to 80 m
- Storage container size: 600 x 400 x 320 mm
- Cargo: up to 30 kg
- Intelligent storage processes
- No relocating necessary
Smart Module
Smart Module
Control software keeps track of stock and orders
- Overview of stock thanks to integrated stock management
- Smart storage strategies
- Cutting-edge user interfaces with high usability
- Intelligent energy management
- Clever security concept
- Clear, easy-to-use system visualisation
Advantages of using PickEngine for your fulfilment
Highest performance
with low personnel costs
5,000 order lines per hour
Ergonomic goods-to-person work stations
Increased employee satisfaction
Train new personnel in just a few minutes
Highest fulfilment quality
and efficiency
Storage of a wide range of items
Fewer errors thanks to automated processes
Intuitive software interfaces for ease of use
Decanting and order fulfilment at a single work station
Complete one-stop solution
All-in-one solution including software
Tried and tested technology
Flexible design
Scalable performance and size
24/7 Service Desk
Highest safety standards: standardized fire safety plan
Fastest system startup on the market
Implementation within 6 months of order placement
Can be integrated into both new and existing buildings
Flexible expansion options
Scalable performance and size
Curious?
Schedule a meeting with our logistics experts today!
Send enquiry now.
To submit the form, Google reCAPTCHA must be loaded.
Google reCAPTCHA privacy policies
Curious?
Schedule a meeting with our logistics experts today!
Send enquiry now.
To submit the form, Google reCAPTCHA must be loaded.
Google reCAPTCHA privacy policies
Unparalleled performance with the PickEngine AS/RS
To ensure that your customers are satisfied, orders need to be fulfilled quickly and without errors. Our automated storage and retrieval system, PickEngine, delivers what the name promises: With the ability to process 5,000 order lines per hour, PickEngine is twice as powerful as comparable systems on the market.
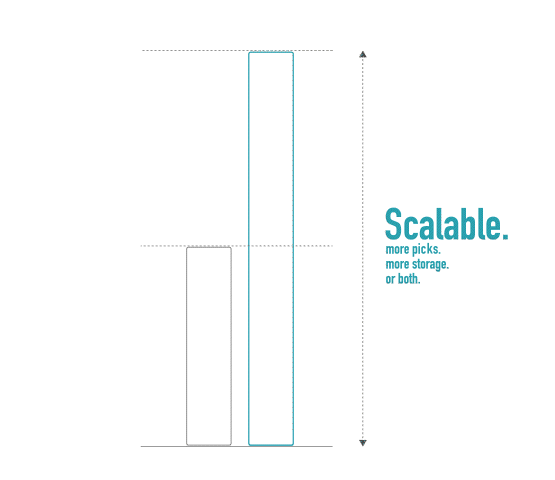
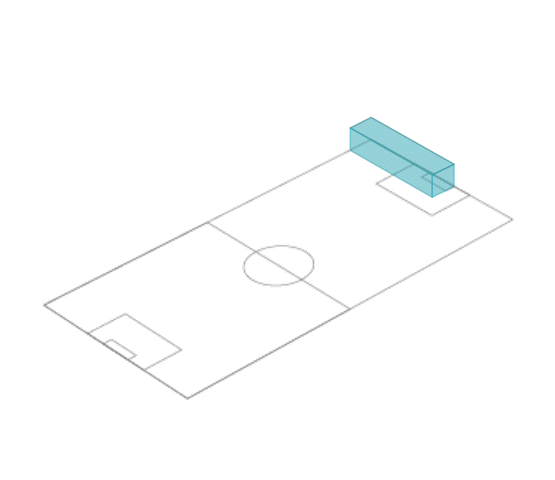
Adapting PickEngine to your needs is as easy as ABC
PickEngine accommodates all your performance and space needs. All you need to do is combine two or more system modules. One module is around five metres wide, ten metres high and scalable in length from 35 to 80 meters. You can string up to ten modules together for maximum efficiency.
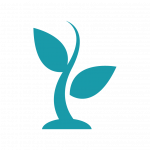
Less floor space occupied,
more storage capacity
With PickEngine you can make the most of your building’s height – with ten metres in height, the system offers more storage capacity while using less floor space.
Our AS/RS can handle a variety of goods, from fashion items, electronic components and cosmetics to food and medicine. Each container measures 600 x 400 x 320 mm and can hold up to 30 kilogrammes of items. In addition, you can use container dividers to increase the containers’ storage density when handling small items.
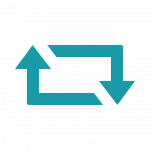
Streamlined processes thanks to
one-touch fulfilment
The PickEngine goods-to-person work stations unite the latest in ergonomics with efficient, error-free order processing to form cutting-edge work stations that handle decanting as well as order picking processes. They help you streamline processes and make your order fulfilment efficient by using personnel effectively.
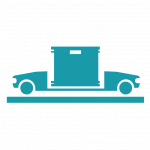
Proven store bot technology
ensures top performance
At the heart of the PickEngine automated storage and retrieval system is KNAPP’s proven shuttle technology. The shuttles are fast storage robots that automatically store and retrieve containers in the rack line systems of the PickEngine. Their movements are coordinated by software to fulfil orders at the right time, changing between rack line systems to reach any container and access any work station in the system.
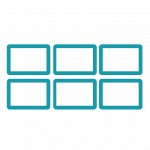
Intelligent software controls, monitors and optimises the system
The PickEngine system includes a sophisticated software solution by KNAPP. The software takes care of a number of tasks: It monitors stock levels and all movements of the storage bots, finds the ideal storage location for every container and optimises storage and retrieval processes to ensure efficiency and save energy.
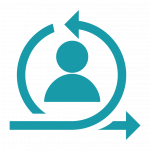
Reliable customer service
around the clock
PickEngine is a robust and low-maintenance AS/RS. Should the need arise, our technical experts at the KNAPP Service Desk are happy to provide assistance around the clock and in eight different languages. In addition, you can select what other services you need from our extensive service portfolio.
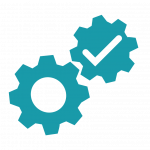
Highest safety and security:
for people and operation
PickEngine is equipped with tested, proven and perfected automation technology and software by KNAPP. Worldwide, there are more than 40,000 storage robots in operation, proving that our AS/RS is both safe and secure. PickEngine is based on a certified safety concept, which ensures highest safety of personnel during maintenance and repair. In addition, the system is set up redundantly so that if a storage robot fails, the other bots can continue to process orders.
About KNAPP
Create added value along the value chain using digital solutions and automation technology. We don’t follow trends at KNAPP. We start them. Do you wish you were closer to your customers or had a more agile supply chain?
Whatever your goals are, we can help you get there with a state-of-the-art, digitally connected value chain. Our automation solutions are setting new standards in the industry and cover the entire value chain: from production and distribution to the last mile including stores where customers can enjoy unique shopping experiences. As a value chain tech partner, it’s our mission to provide our customers with the technologies they need to excel in their industry: Our portfolio includes the latest shuttle technology, robotics infused with artificial intelligence, all-in-one software solutions and more.
We are a strong partner and as such, we support projects on all levels, starting from consulting, planning and system implementation to maintenance and life cycle management. Successful companies such as adidas, Zalando, Würth, Kroger, Woolworths, McKesson and Luxottica rely on our partnership and expertise. Over 3,000 of our automated systems are in operation worldwide, creating added value for our customers in their distribution networks.
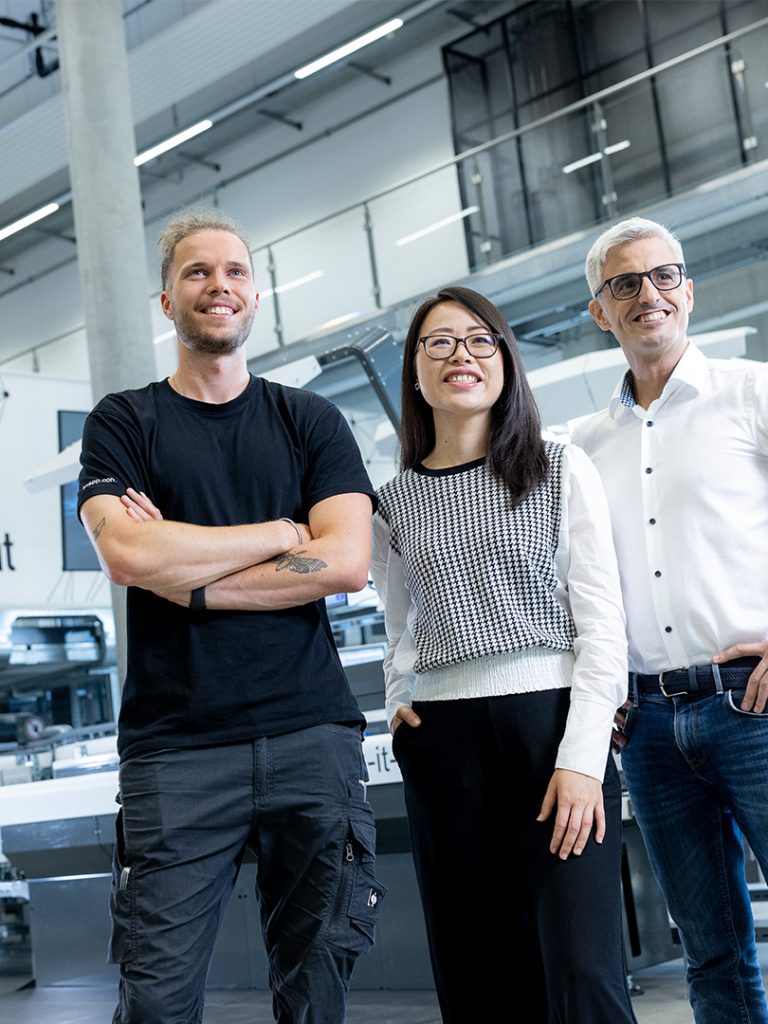